Drilling Fluid in Oil and Gas Operations: Your Essential Guide
Drilling fluids, often referred to as drilling mud, are far more complex than their nickname suggests. These carefully engineered mixtures play a multifunctional role in oil and gas operations, directly influencing drilling efficiency, safety, and well integrity. From transporting rock cuttings to maintaining downhole pressure, drilling fluids are the workhorses of successful drilling operations. In this comprehensive guide, we'll explore the world of drilling fluids, their types, functions, and how they are selected for optimal performance.
What Is Drilling Fluid in Oil and Gas?
Think of drilling fluids as the lifeblood of any drilling operation! The mud is pumped down the wellbore during drilling, serving multiple critical purposes. Here's a breakdown of their key purposes within a wellbore:
Transporting Cuttings: As the drill bit crushes rock, drilling fluid flushes these cuttings away from the bit face and carries them upwards to the surface.
Controlling Wellbore Pressure: Drilling fluids are designed with a specific density (mud weight) to prevent uncontrolled influx (kick) or loss of formation fluids (lost circulation).
Cooling and Lubricating the Drill Bit: Fluids dissipate heat away from the bit and reduce friction, prolonging the lifespan of the drill bit.
Stabilizing the Wellbore: The fluid creates a thin, impermeable barrier (filter cake) on the wellbore wall to prevent the wellbore from collapsing, especially in reactive shale formations.
What Fluid Is Used in Drilling?
Drilling fluids fall into three main categories: Water-Based Muds (WBMs), Oil-Based Muds (OBMs), and Synthetic-Based Muds (SBMs). Each category offers distinct advantages and disadvantages, making the choice highly dependent on the specific drilling conditions and goals. Here's a breakdown of each type's specifications and applications:
Water-Based Muds are the most common and generally the most cost-effective type of drilling fluids. As the name suggests, they use water as the base fluid, along with various clays, polymers, and other additives to achieve the desired properties. WBMs are often preferred for their environmental friendliness and ease of handling. However, they can have limitations in challenging high-temperature, high-pressure formations and may not be suitable for drilling through highly reactive shale sections.
Oil-Based Muds use oil as the base fluid, typically diesel or mineral oil. OBMs offer superior performance in demanding environments such as high-pressure, high-temperature (HPHT) wells. They also provide excellent lubrication and shale inhibition, minimizing wellbore instability. The downside of OBMs is their potential environmental impact and higher costs compared to WBMs.
Synthetic-Based Muds provide a middle ground, combining the performance advantages of OBMs with reduced environmental impact. SBMs use specially designed synthetic fluids as their base, offering superior drilling performance while being more biodegradable and less toxic than traditional oil-based muds. While still more expensive than WBMs, the cost difference between SBMs and OBMs has narrowed due to technological advancements.
What Are Drilling Fluid Additives?
Drilling Fluid Additives are specialized chemicals or materials added to drilling fluids to enhance their properties and address specific challenges encountered during drilling operations. They provide a high degree of customization, allowing engineers to fine-tune fluid properties like viscosity, density, and filtration control to suit operational needs of each drilling project.
Types of Drilling Fluid Additives
As stated before, drilling fluid additives are essential for successful drilling operations and addressing specific downhole challenges. As might be expected, they come in different types to suit specific applications and needs. The following is an overview of their more common types and their functions:
Lubricants: Reduce friction and torque within the wellbore, especially in deviated drilling and troublesome formations. This ensures smooth operation, extends the life of the drill string and bit, and is essential within shale sections requiring lubricity.
Shale Inhibitors: Minimize swelling and instability in shale formations, preventing wellbore problems, and maintaining stability.
Defoamers: Control and reduce unwanted foam formation for efficient fluid circulation.
Biocides: Inhibit bacterial growth that can degrade drilling fluid properties and equipment.
Corrosion Inhibitors: Protect drilling equipment and downhole tools from corrosive fluids.
Fluid Loss Additives: Minimize the loss of drilling fluids into the formation, maintaining mud properties and preventing formation damage. Examples include filtration control additives, lignite drilling mud additives, lignosulfonate drilling mud, and starch drilling fluid additives.
Polymers (Polymer Drilling Fluid Additives): Enhance viscosity, fluid-carrying capacity, and provide filtration control. Examples include hec drilling fluid additives.
Specialty Additives: A wide range of additives for specific needs such as weighting materials, viscosifiers, and more. Some of the examples include soil-based mud additives, Soltex drilling mud additives, and gilsonite drilling mud additives.
Difference Between Drilling Fluid and Drilling Mud
The terms drilling fluid and drilling mud are often used interchangeably. However, drilling mud is a broader term that encompasses all types of fluids used in drilling, including water-based, oil-based, and synthetic-based fluids.
Drilling Mud Types
Within the broader categories (WBM, OBM, SBM), there are numerous drilling mud types tailored to meet various drilling environments. Some common examples include:
Basic WBMs: Simple mixtures used for shallow wells with minimal issues.
Polymer-based WBMs: Polymers enhance viscosity and fluid loss control.
High-Performance WBMs: Designed for HPHT drilling and severe conditions.
Inhibitive WBMs: Contain salts and polymers to minimize shale swelling.
Conventional OBMs: Traditional oil-based muds using diesel or mineral oil base.
Low-toxicity OBMs: Utilize less harmful base oils for reduced environmental impact.
SBMs: Combine performance benefits with greater environmental compatibility through specifically designed synthetic base fluids.
Choosing the Right Drilling Fluids
When selecting drilling fluid additives (also called drilling mud additives or simply drilling additives), factors like rock formation type, fluid base (water, oil, synthetic), as well as environmental regulations (environmentally sensitive areas might require SBMs or MBMs with strict biodegradability standards) play a critical role in choosing the right additive chemistry and concentration (aka additive drilling material). Additionally, the type of well (vertical, horizontal, etc.), target depth, and complexity of the wellbore design necessitate specific fluid features.
TEAM Chemicals: Your Drilling Fluid Solutions Provider
TEAMChem understands the complexities of choosing the right drilling fluids and is dedicated to providing you with the optimal solutions for your oil and gas operations. We offer:
Comprehensive Product Portfolio: A wide range of WBMs, OBMs, SBMs, and a rich selection of specialty drilling fluid additives to meet your needs.
Technical Expertise: Our team of fluid engineers helps you select the right fluids, tailor them, and provide ongoing support for optimal performance.
Reliable Supply: Our supply chain ensures you have the drilling fluids and additives you need, when you need them, minimizing downtime.
Competitive Pricing: We offer top-quality drilling fluid solutions at competitive prices, ensuring you get the value you deserve.
Commitment to Safety and Sustainability: TEAMChem prioritizes environmentally responsible products and practices, helping you maintain regulatory compliance and reduce your environmental footprint.
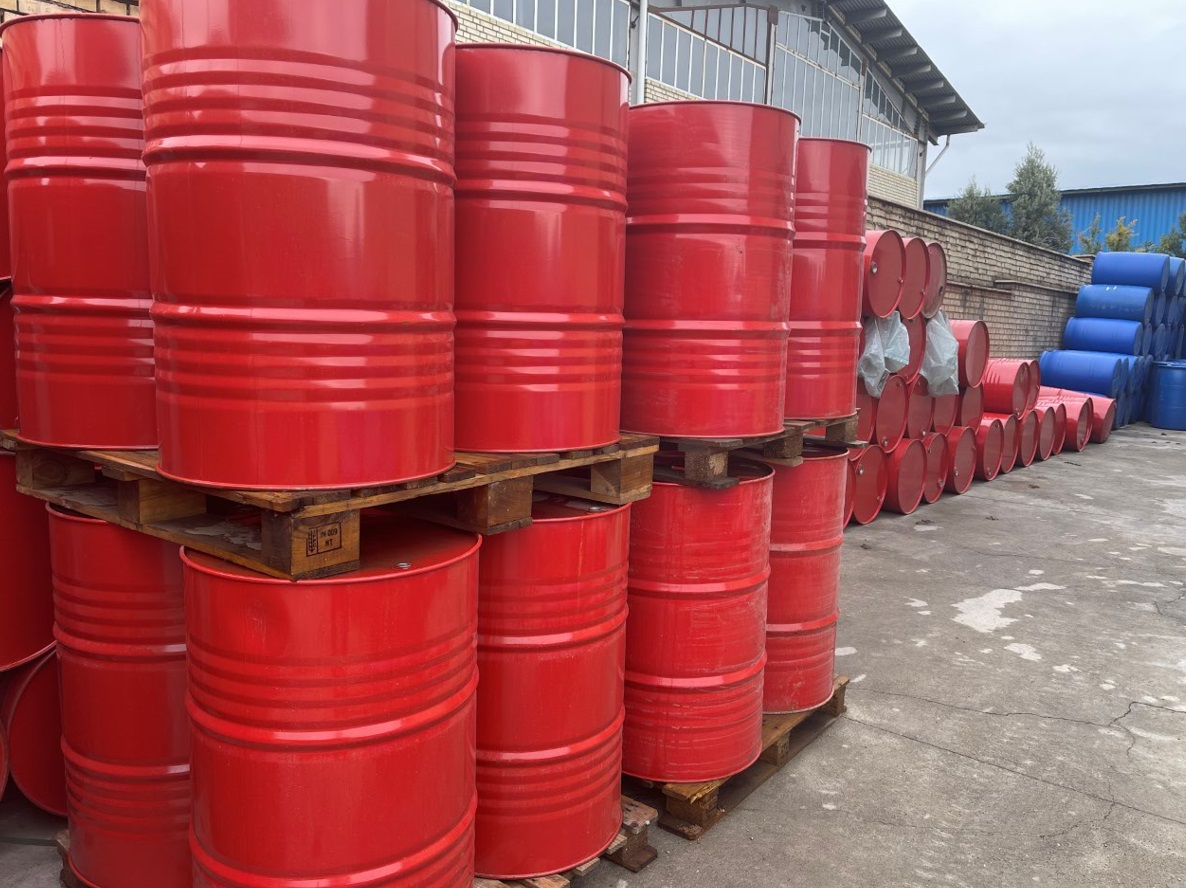
TEAM Chemicals: Your Drilling Fluid Solutions Provider
Call to Action
Ready to optimize your drilling operations with the right drilling fluids? Contact TEAMChem today! Our experts at TEAMChem are your partners in success, ready to provide customized drilling fluid solutions to help you achieve efficient, safe, and cost-effective drilling.