From the gleaming exterior of cars to the protective coating on bridges, barite, a naturally occurring mineral, plays a surprisingly important role in creating the paints we rely on. This versatile material is an excellent weighting agent, enhances gloss control, provides a smooth finish, and improves the durability and scratch resistance of paints and coatings we know and use. This article delves into the world of barite, highlighting its applications within the paint industry, the advantages it provides, the critical role it plays in creating exceptional paints and coatings, and its promising future in the sector.
What is Barite?
Barite, also known as baryte, is a dense, white or colorless mineral composed of barium sulfate (BaSO4). It occurs naturally and is mined from extensive deposits found worldwide. Barite possesses a unique combination of properties that bring several advantages to coatings, such as:
High Density: With a specific gravity of around 4.5, barite is among the densest non-metallic minerals. This exceptional density is crucial for applications where weight is a significant factor.
Chemical Inertness: Barite is highly resistant to acids, alkalis, and most solvents. This inertness ensures the stability of paint formulations and long-term coating performance.
Low Oil Absorption: Barite doesn't easily absorb liquids, making it an outstanding filler material. Low oil absorption translates to optimized resin interactions and predictable paint formulation behavior.
Excellent Whiteness and Brightness: Its color properties enhance coating aesthetics. Pure barite's white or colorless nature makes it ideal for use in bright paints and coatings.
Low Abrasiveness: Barite's softness minimizes wear and tear on processing equipment. This reduces maintenance costs and potential downtime for paint manufacturers.
Key Applications of Barite in the Paint Industry
Paint and coating formulators turn to barite to solve specific challenges and achieve desired outcomes. Its above-mentioned characteristics contribute to enhanced durability, cost optimization, and specialized applications.
Filler and Extender: Barite's primary function in paints is as a filler and extender. Fillers add bulk to paint formulations, increasing volume and reducing costs. As an extender, barite helps replace more expensive prime pigments like titanium dioxide (TiO2), optimizing cost-efficiency. It's important to balance barite as a filler/extender, ensuring it doesn't diminish critical performance properties.
Density Enhancement: Due to its high density, barite significantly increases the weight and density of paints and coatings. This characteristic is particularly useful in applications where increased weight is desirable, such as:
Marine Paints: Increased density helps marine coatings withstand the harsh marine environment with its dynamic forces, saltwater, and potential for biofouling.
Radiation-Shielding Coatings: Barite is a key component in coatings for X-ray rooms and facilities handling radioactive materials, where its density blocks harmful radiation.
Viscosity and Flow Control: Barite modifies the viscosity and flow properties of paints, facilitating smooth application and uniform finishes. The proper selection of barite grade can assist in achieving targeted viscosity for different application methods, whether by brush, roller, or spray systems.
Gloss Control: The particle size of barite influences the final coating's gloss level. Fine barite particles promote superior gloss, while coarser grades can provide matte, textured, or satin finishes. This allows tailoring of coatings for specific aesthetic requirements.
Durability Enhancement: Barite improves coatings' hardness, scratch resistance, weather resistance, and chemical resistance. Its inclusion strengthens the coating matrix, providing a more resilient shield against the elements and mechanical wear.
Types of Barite Used in the Paint Industry
To cater to diverse paint and coating requirements, barite undergoes processing to achieve specific characteristics. Here's an overview of its common types:
Natural Barite: This type is minimally processed, derived from crushing and grinding natural barite ore. It's suitable for general-purpose fillers and extenders where color and extreme purity are less critical.
Precipitated Barite: This synthetic barite is produced through a controlled chemical reaction. Precipitated barite is much finer, purer, and has a more consistent particle size distribution, making it ideal for demanding applications requiring superior performance. Its controlled production process can yield barite with precisely tailored attributes.
Micronized Barite: This involves grinding barite to ultrafine particle sizes. Micronized barite offers enhanced smoothness, dispersibility, and exceptional optical properties. It's often employed in applications demanding the highest levels of gloss, smoothness, or where barite's presence must be visually undetectable.
Barite's Use in Different Paint and Coating Formulations
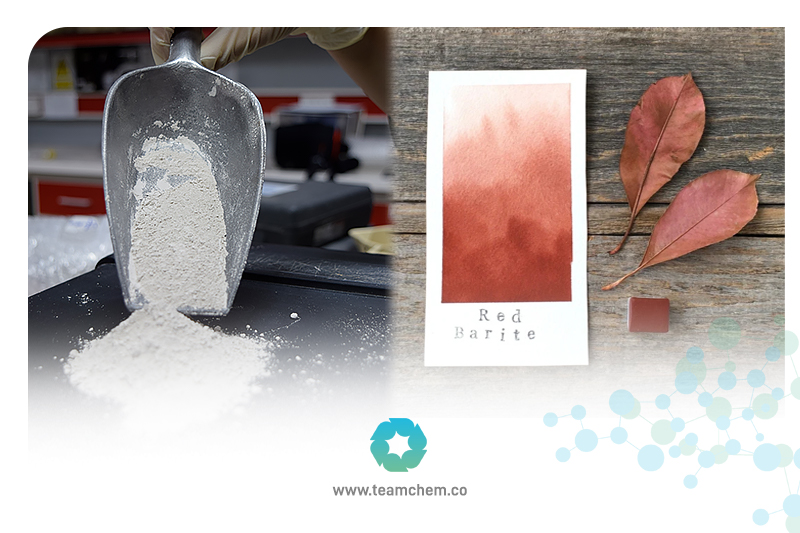
While barite's widespread use in modern paints might feel contemporary, its presence in coatings stretches back centuries. This versatile mineral has consistently found ways to enhance the performance and aesthetics of multiple paints and protective finishes:
Primers: Barite enhances primer adhesion, density, and corrosion resistance. In primers for metal substrates, barite can displace moisture and oxygen, reducing the potential for rust and extending the lifespan of the coating system.
Decorative Paints: Barite promotes a smooth finish, gloss control, and durability. Its use in everything from interior wall paints to automotive topcoats contributes to long-lasting, visually appealing finishes.
Industrial Coatings: Barite offers chemical resistance, abrasion resistance, and density enhancements for heavy-duty coatings. Specialized industrial coatings used in chemical plants, oil refineries, or on exposed infrastructure may rely on barite's inertness and hardness for extreme environment protection.
Marine Paints: Barite's increased density helps marine paints resist the harsh marine environment and withstand the force of ocean waves, preventing corrosion. Barite also helps impede the growth of marine organisms on ship hulls, reducing drag and improving fuel efficiency.
Powder Coatings: Barite promotes flowability, uniform thickness, and gloss. In powder coatings, barite contributes to even coverage during application and a cured finish that meets specific visual and performance needs.
Radiation-Shielding Coatings: Barite's high density makes it suitable for applications requiring radiation shielding. These specialized coatings are used in medical facilities, nuclear plants, and other environments where controlled exposure to radiation is essential.
Benefits of Using Barite in Paints and Coatings
Barite is like the Swiss Army knife of paint ingredients. It tackles a range of tasks simultaneously: controlling cost, boosting durability, optimizing texture, and much more. This multifaceted mineral streamlines your formulations and empowers your coatings. Here’s a breakdown of some of barite’s key advantages:
Cost Savings: Barite helps reduce paint cost by replacing expensive components. For optimal cost-efficiency in paint formulations, experts like TEAMChem specialize in sourcing the right barite grades to meet your specifications.
Improved Performance: Barite strengthens coatings by enhancing durability and resistance. Barite-fortified coatings are less prone to cracking, chipping, and fading even in demanding conditions.
Enhanced Properties: Barite modifies flow, gloss, density, and other properties for greater control over coating characteristics. This versatility allows fine-tuning of coatings for specific use cases.
Environmentally Friendly: Barite is non-toxic and chemically stable. Its use in paints can aid in substituting for certain components that may have harsher environmental impacts.
Versatility: Barite is compatible with various resins and binders, making it a flexible ingredient in a wide range of paint chemistries.
Global Availability: Abundant barite reserves ensure a reliable supply, contributing to consistent availability for paint and coating manufacturers.
Factors Affecting the Performance of Barite in Paints
The effectiveness of barite as a paint and coatings ingredient isn't a given. Several crucial factors, from its particle size to its compatibility within the formulation, determine how well barite will ultimately enhance your coatings' performance.
Particle Size Distribution: The particle size and its distribution significantly influence gloss, dispersion, and final coating properties. Finer barite leads to high gloss finishes, while coarser particles can influence texture. Optimizing this characteristic is crucial for achieving the desired finish.
Purity and Whiteness: The presence of impurities can impact coat color and performance. Higher-purity barite is necessary for bright white paints and critical applications. Impurities can affect long-term color stability and the coating's resilience.
Oil Absorption: Lower oil absorption levels are generally preferred for optimal resin-barite interaction and paint formulation stability. High oil absorption might necessitate the use of additional dispersants or resins, impacting formulation cost and behavior.
Chemical Compatibility: Ensure the selected barite grade is compatible with the binder, resin, and other ingredients in the paint formulation. Incompatibility could lead to clumping, instability, or unpredictable coating properties.
Global Barite Market and Leading Suppliers
The global barite market is substantial, driven by demand from diverse industries, including paint and coatings, oil and gas drilling, and various other applications. Major barite producing countries include:
China: The world's dominant barite producer.
India: Holds significant barite reserves and is a major producer.
United States: A leading supplier of barite, particularly in certain states like Nevada.
Morocco: A growing force in the global barite market.
Mexico: Possesses substantial deposits and is a notable barite producer.
Other notable barite-producing countries include Iran, Turkey, Thailand, Kazakhstan and Pakistan.
The barite supply chain for paints and coatings involves several types of players, each with a distinct role:
Mining Companies: These companies extract and process raw barite ore. Major players include:
Excalibar Minerals LLC (US)
Halliburton (US)
Andhra Pradesh Mineral Development Corporation (India)
Specialty Processors: These companies often purchase barite from miners and further process it to achieve specific grades and characteristics required by the paint industry (e.g., precipitated barite, micronized barite).
Mil-Spec Industries Corporation (US)
Shandong Xintai Barite Co., Ltd. (China)
Distributors and Traders: These companies facilitate the movement of barite from mining locations or processing centers to paint manufacturers. They specialize in logistics, quality control, and market intelligence. Some examples include:
SinoBarite (China)
Tricon Colours (US)
Paint Manufacturers: The end-users of barite. They incorporate barite into their formulations to achieve the desired performance and cost characteristics in their paints and coatings. Major paint manufacturers include:
Sherwin-Williams
PPG Industries
AkzoNobel
Optimizing the Use of Barite in Paint Formulations
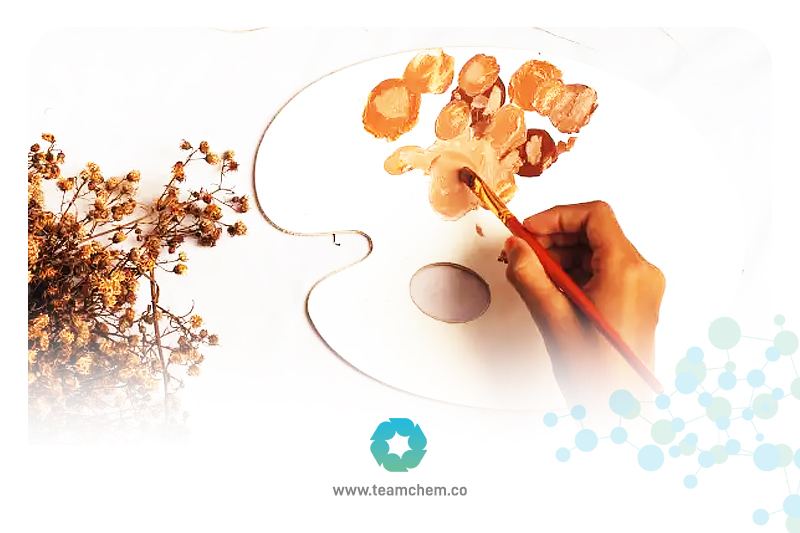
Optimizing barite use means going beyond simple inclusion. Strategic approaches in barite selection, incorporation, and formulation adjustments lead to paints and coatings that deliver superior performance, cost-effectiveness, and consistency. Here are some tips for optimizing the use of barite in paint formulations:
Selecting the Right Barite Grade: Choose barite with the particle size, purity level, and chemical characteristics aligned with the desired coating properties and specifications. Partnering with a supplier like TEAMChem ensures you have access to a comprehensive range of barite options to achieve your paint and coating objectives.
Proper Dispersion: Ensure barite is adequately dispersed into the paint formulation to avoid clumping and achieve homogeneous distribution. Excellent dispersion maximizes surface area interaction with other components,contributing to optimal performance.
Formulation Considerations: Balance barite with other ingredients like titanium dioxide and other fillers to optimize cost and performance characteristics. A skilled formulator can achieve the ideal synergy for the desired outcome.
Quality Control: Stringent quality testing can ensure barite meets specifications and maintains consistent paint quality. This consistency is vital in large-scale paint manufacturing.
The Bright Future of Barite in the Paint Industry
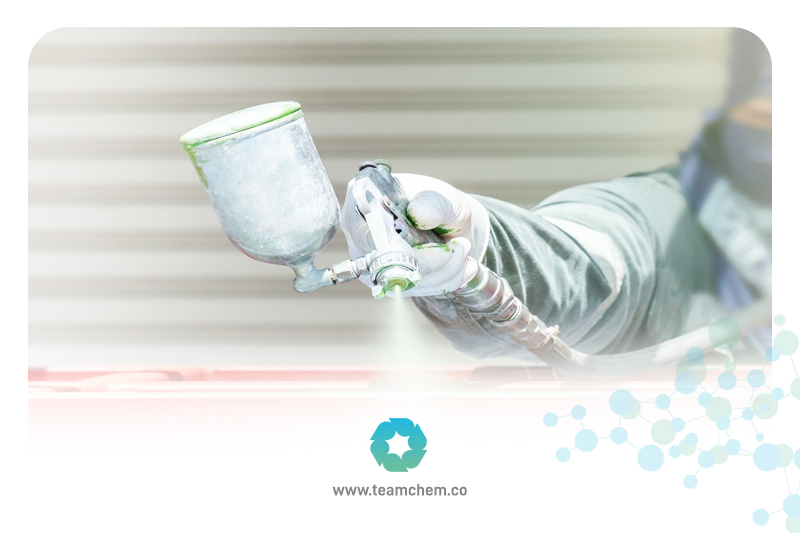
The future of barite in the paints and coatings industry is intertwined with broader economic trends, technological advancements, and the sector's ever-evolving needs. While the specifics may change, barite's unique properties and adaptability ensure it will continue to be an essential contributor to creating the paints and coatings of the future. Here's TEAMChem’s breakdown of potential pathways for barite's evolution and expanded use within the paint and coatings industry:
Process and Product Innovation
Ultra-Fine and Nano-Sized Barite: Advancements in grinding technology could lead to even finer grades of barite, unlocking applications demanding exceptional smoothness, transparency, or unique surface effects in coatings.
Surface Functionalization: Treating barite surfaces with specific chemistries could tailor its interaction with resins and other paint components, potentially boosting dispersion, controlling rheology, or providing specific functionalities.
Hybrid Fillers: Combining barite with other fillers or additives could create synergistic effects, leading to performance enhancements beyond what barite can achieve alone.
Focus on Sustainability
Recycled Barite: Establishing reliable sources and processing methods for recycled barite offers a more sustainable option for coatings manufacturers. This aligns with the growing emphasis on circular economies.
Barite from Alternative Sources: Exploration into using barite derived from mine tailings, industrial byproducts,or even engineered barite could open up more environmentally conscious supply chains.
Formulation Leverage: Optimizing formulations to maximize barite's effectiveness, allowing formulators to reduce or replace components with more significant environmental impact.
Expanding Applications
High-Performance Coatings: Barite's potential lies in advanced coatings designed for extreme corrosion resistance, chemical containment, high temperatures, or harsh weather conditions.
Multi-Functional Coatings: Barite could play a role in coatings beyond just filling and density modification.Examples include:
Anti-fouling marine coatings: Barite's density and potential surface treatments could make it an ingredient in coatings preventing aquatic organism buildup.
Thermal Management: Barite in thermally conductive or insulative coatings for energy management purposes.
Radiation shielding: Barite's high density is already used in some radiation-related coatings, and refinements could further this application.
Collaboration and Market Dynamics
Partnerships Between Suppliers and Paint Manufacturers: Close collaboration could encourage tailored barite development, opening new opportunities for specialized coating solutions.
Global Market Shifts: Staying attuned to emerging barite-producing regions, trade policy changes, and innovation hubs will be crucial for companies involved in the barite supply chain.
Ready to Elevate Your Coatings? TEAM Chemicals is Your Barite Solution
Are you looking to enhance your paint and coatings formulations while maintaining cost-effectiveness? The unique properties of barite and the expertise of TEAMChem offer a powerful combination for achieving superior coatings performance. TEAMChem helps you by:
Maximize Barite's Potential: TEAMChem understands the nuances of barite. We source and supply a comprehensive range of barite grades, including natural, precipitated, and micronized varieties, to meet the diverse needs of the paints and coatings industry.
Solutions-Driven Approach: Our team doesn't just provide barite; we offer solutions. We partner with paint formulators to optimize the selection and integration of barite, ensuring it delivers maximum value within your specific coatings systems.
Tailored for Your Needs: Whether you require barite for density enhancement, viscosity control, improved durability, or a combination of benefits, TEAMChem helps you find the right fit for your formulations and performance goals.
Quality and Consistency: We prioritize rigorous quality control to ensure the barite you receive consistently meets demanding specifications, assuring predictable performance in your paints and coatings.
Transform your coatings. Contact TEAMChem today and discover the barite advantage!